
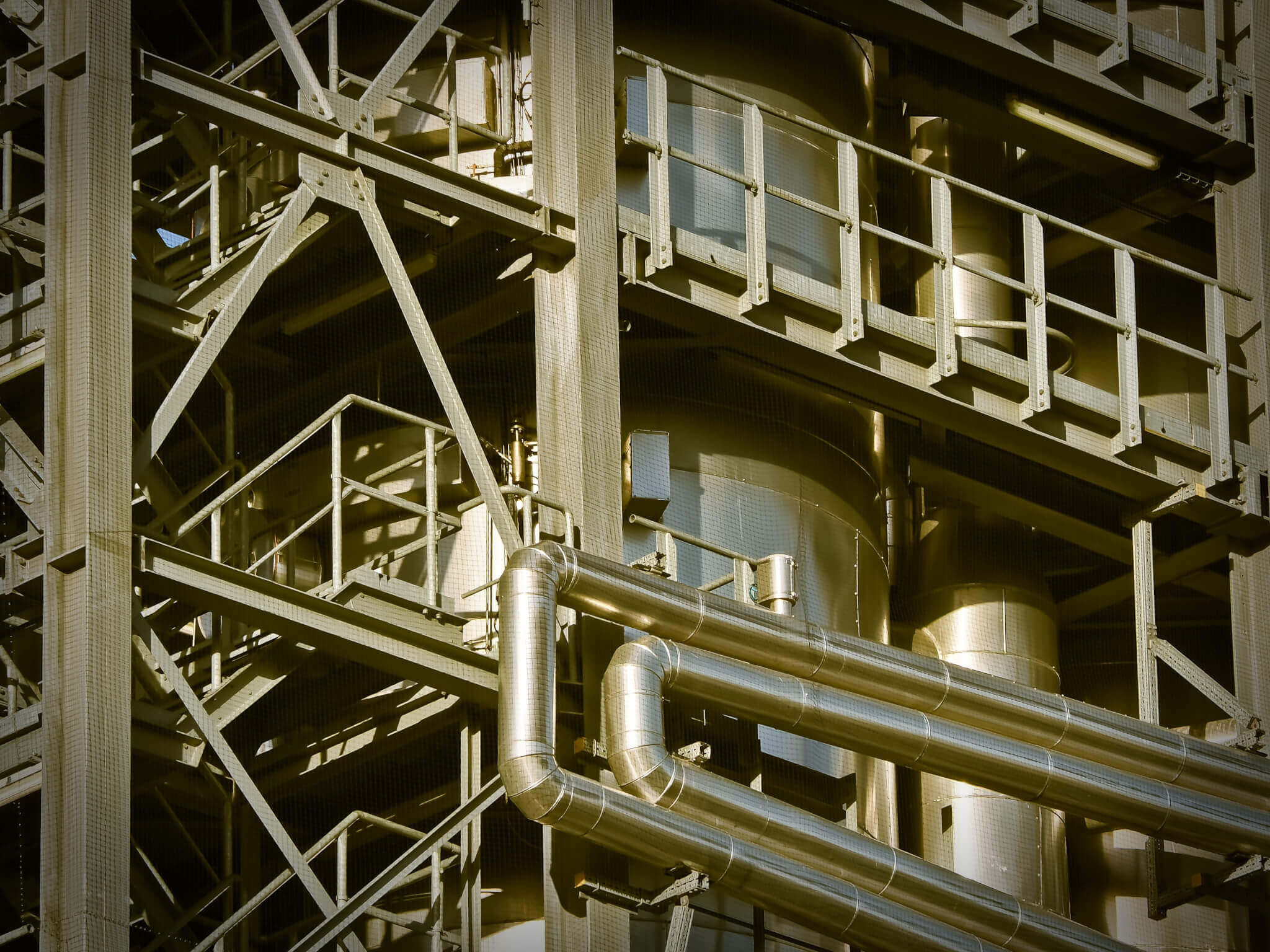
Here catalyst size and morphology as well as support and additives matter as well. Examples are CO oxidation as well as partial and selective oxidation of hydrocarbons over noble metals and metal oxides. Oxidizing and reducing species may lead to oxidation (reduction) of the few top monolayers of the catalyst and even oxidize (reduce) the entire catalytic particle. Depending on the species’ partial pressures in the gas phase a strong adsorbate may cover the entire catalytic surface and inhibit catalytic reactions (CO on Pt in low-temperature fuel cells). On the other hand, adsorbing radicals may quench chemical reactions in the gas-phase such as in the suppression of explosions in catalytic micro reactors. For instance, desorbing OH from Pt can enhance homogeneous ignition in the gas phase in catalytically supported combustion. Desorbing intermediates and radicals may trigger chemical reactions in the gas-phase and by this open a competing reaction pathway. Examples are the water molecule in partial oxidation of alkanes over noble metals and NO 2 in NO x storage catalysts.

However, intermediates formed on the surface may desorb as well and re-adsorb. The obvious direct chemical interaction of the gas-phase with the catalytic surface is the adsorption of reactants from and desorption of products to the gas phase. The catalyst itself may be modified in time by interaction with species from the gas phase the catalytic particles can be oxidized, reduced, aged, poisoned, regenerated, evaporated etc.Ī variety of chemical and physical interactions of processes in the gas-phase with the catalytic surfaces are sketched in a more systematic way in Fig. Temporarily and spatially varying feed composition and heat transfer between reactor and ambience will cause a non-uniform temperature distribution over the entire monolith, and the behavior will differ from channel to channel. The temperature distribution depends on the interaction of heat convection and conduction in the fluid, heat release due to chemical reactions, heat transport in the solid material, and thermal radiation. Due to the high temperatures, the chemical species may also react homogeneously in the gas phase. The products and intermediates desorb and diffuse back into the bulk flow. The reactants diffuse to the inner channel wall, which is coated with a porous structure (washcoat) supporting the catalytic material, through which gaseous species diffuse to eventually react on the catalytic particle. In each channel of the monolith, the transport of momentum, energy, and chemical species occurs not only in flow (axial) direction, but also in radial direction. Figure 1 illustrates the physics and chemistry in a catalytic combustion monolith that glows at a temperature of about 1,300 K due to the exothermic oxidation reactions. They are frequently used for the reduction of pollutant emissions from automobiles, selective oxidation and reforming of hydrocarbons, and combustion of natural gas. Catalytic monoliths can serve as an example. A variety of physical and chemical processes in the gas-phase of a catalytic reactor influences conversion and selectivity as well as short and long-term catalyst performance. The interaction of the catalytic surface with the gas phase in heterogeneous catalysis implies much more than the simple textbook scheme of providing reactants and delivering the products by mass diffusion.
